Custom Moulding Process
We wanted to walk you through our process for creating Custom Mouldings. This process reflects how careful we are with your Hardwood Moulding’s creation. We are showing our South Carolina location but we have all of the same capabilities at our Washington State location as well.

1. First, we receive a moulding order from a customer including either a drawing or sample of the moulding needed. The example we show in this series are for a six-inch Sapele Wood Moulding. We then check if we have a matching moulding knife on hand. If not, we create one to match you specifications exactly. For this project, we had the moulding knife on hand.
2. The first step is to hand sort and inspect the wood to be used. We sort boards to allow for the least amount of waste and the best appearance possible for your final products. For this project, we are making a 6 inch tall speed base so we will sort out boards that are 6.5-8″ to minimize wood waste and it allows us pass those saving on to our customer.
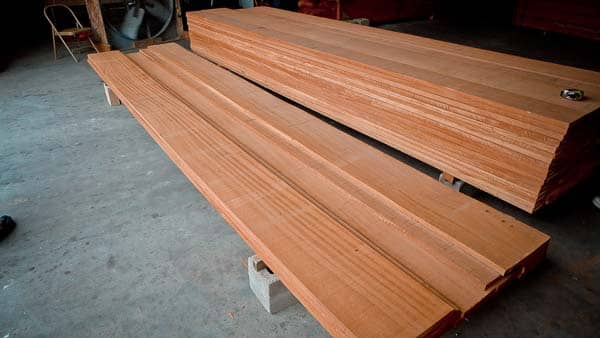
Sorting Sapele to be made into moulding
3. Next, the boards are planed down to smooth the rough finish that comes with our direct imported rough lumber. We set this up using less expensive wood as set-up pieces and confirm the board thickness after planing using vernier calipers to make sure the thickness is exactly as needed for moulding.
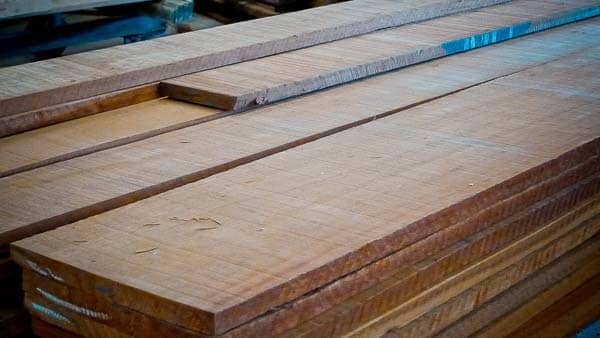
Rough boards as they are pulled from our warehouse
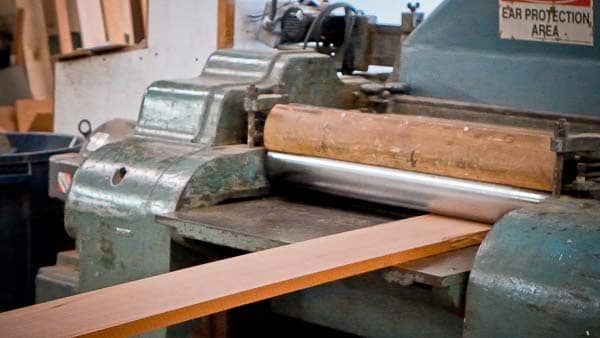
Smooth board coming out of the planer
4. Then we gang rip (gang saw) the wood to width to ensure that it is a smooth finished board at the correct width. At this point, we also use a set-up pieces and confirm the boards proper width.
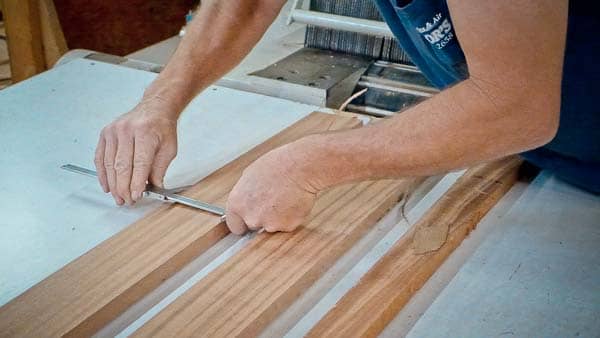
Checking board width after being gang ripped
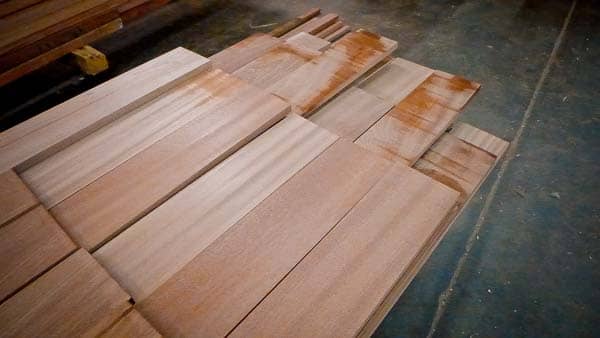
Planned and Ripped boards ready to move onto the Moulder
5. We mount the milling blade onto head and make sure that is exactly straight to assure no skew in the moulding.
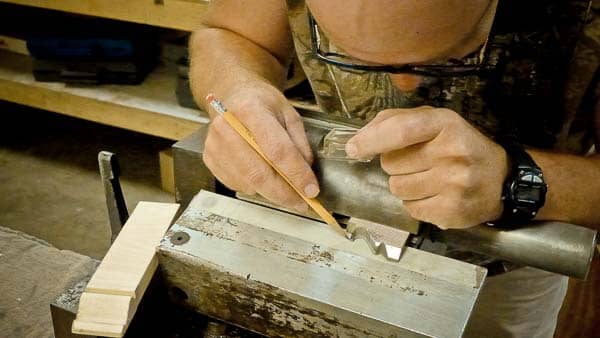
Mounting and checking the moulding blade
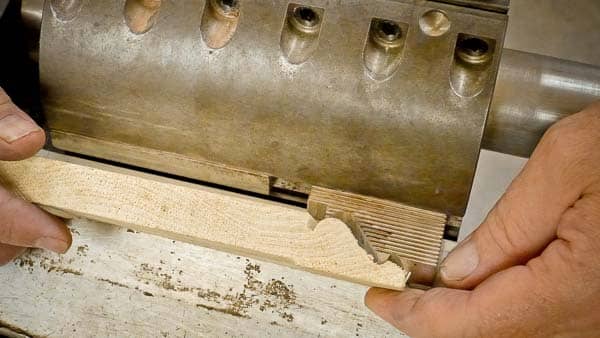
Checking blade against moulding sample on hand
6. Once the head and blade are mounted in the moulding machine we then run through a less expensive wood as set-up pieces and confirm the board width, thickness, and any other specific dimensions using vernier calipers to make sure the moulding matches the customer sample or drawing exactly.
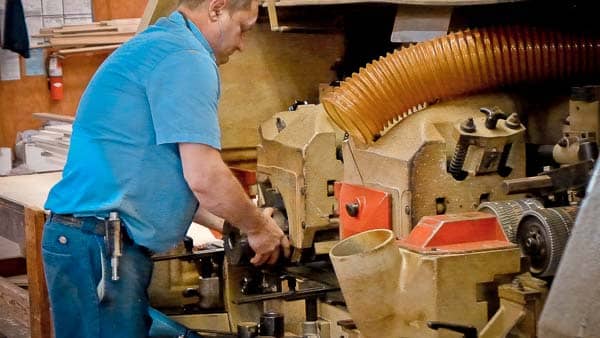
Mounting blade and head in to the moulder
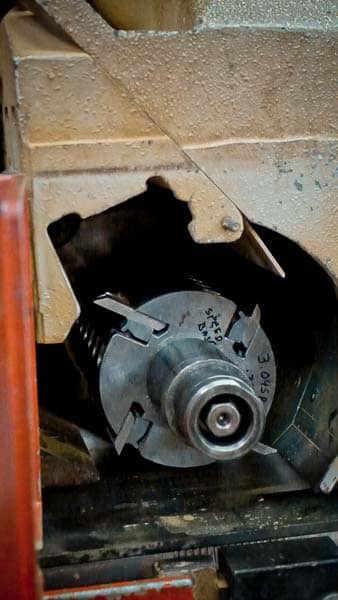
Blade and head in the moulder
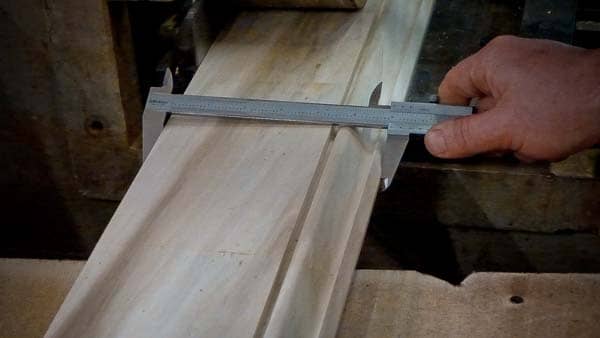
Checking set-up piece to make sure that it is the proper dimensions.
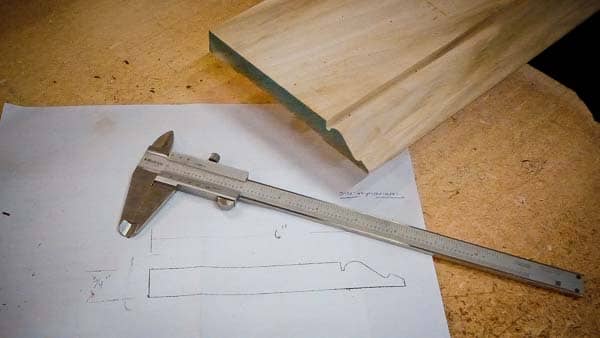
Moulding set-up piece and the drawing.
7. As we will mould each piece, we make sure to run at slower speed to avoid any chattering or damage from the milling process and we closely inspect each piece of moulding as it comes off the machine.
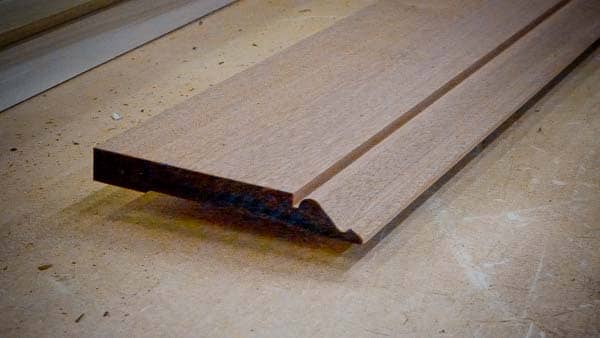
Final Sapele Moulding as it comes off the Moulder.
8. Once the mouldings are all complete, the are plastic wrapped and prepared for shipping to their final destination with care to assure there is no damage to any of the products.
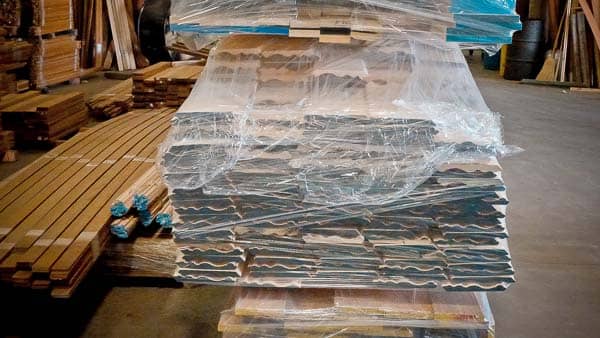
Mouldings plastic wrapped and ready to ship out.
This is our process for creating custom mouldings. We can create custom mouldings in all of our hardwood products for any of your needs. If you have any questions, feel free to contact us or comment below.
Wood Species Guide
Natural woods vary in performance characteristics from one another. This wood comparison chart helps you compare hardness, weight, fungal resistance, and more. Use the wood comparison guide to help you find the right wood for your project.
Locations
Locations are strategically placed throughout the United States to serve our customers. Products stocked at each location are different based on customer needs.